What is Porosity in Welding: Secret Elements and Their Impact on Weld Top Quality
Porosity in Welding: Identifying Common Issues and Implementing Best Practices for Avoidance
Porosity in welding is a pervasive concern that frequently goes undetected until it causes considerable troubles with the stability of welds. In this conversation, we will certainly discover the key variables adding to porosity development, analyze its detrimental impacts on weld performance, and talk about the ideal practices that can be adopted to minimize porosity event in welding processes.
Typical Root Causes Of Porosity

Another constant wrongdoer behind porosity is the presence of impurities on the surface area of the base metal, such as oil, oil, or rust. When these impurities are not properly eliminated before welding, they can vaporize and become caught in the weld, causing issues. In addition, utilizing filthy or wet filler products can introduce contaminations right into the weld, adding to porosity issues. To minimize these common causes of porosity, thorough cleansing of base metals, proper securing gas option, and adherence to optimum welding parameters are vital techniques in attaining high-grade, porosity-free welds.
Effect of Porosity on Weld Top Quality

The presence of porosity in welding can significantly compromise the architectural stability and mechanical homes of welded joints. Porosity produces gaps within the weld steel, weakening its overall toughness and load-bearing capacity.
One of the primary consequences of porosity is a decrease in the weld's ductility and sturdiness. Welds with high porosity levels have a tendency to display lower impact strength and lowered capability to warp plastically prior to fracturing. This can be particularly worrying in applications where the bonded elements are subjected to dynamic or cyclic loading conditions. Moreover, porosity can hamper the weld's capability to properly transfer forces, resulting in early weld failure and prospective security risks in crucial frameworks.
Finest Practices for Porosity Prevention
To enhance the architectural integrity and high quality of other welded joints, what details measures can be carried out to reduce the event of porosity throughout the welding procedure? Making use of the appropriate welding method for the details investigate this site material being welded, such as changing the welding angle and gun placement, can further prevent porosity. Routine examination of welds and immediate removal of any type of issues identified during the welding procedure are crucial practices to avoid porosity and produce top notch welds.
Value of Proper Welding Methods
Applying correct welding methods is paramount in making sure the structural integrity and top quality of welded joints, constructing upon the structure of effective porosity prevention actions. Welding methods directly impact the total stamina and longevity of the welded framework. One key element of appropriate welding methods is preserving the right warmth input. Extreme heat can cause increased porosity due to the entrapment of gases in the weld pool. On the other hand, not enough heat may result in incomplete fusion, creating potential powerlessness in the joint. Additionally, making use of the appropriate welding criteria, such as voltage, existing, and take a trip rate, is important for achieving audio welds with very little porosity.
In addition, the choice websites of welding process, whether it be MIG, TIG, or stick welding, should straighten with the specific requirements of the project to make sure optimal results. Proper cleaning and preparation of the base metal, along with picking the appropriate filler product, are additionally essential parts of proficient welding techniques. By adhering to these ideal techniques, welders can decrease the risk of porosity development and create high-grade, structurally audio welds.
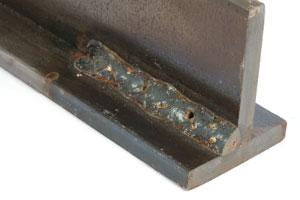
Testing and Quality Assurance Measures
Quality assurance actions play an essential role in verifying the honesty and integrity of welded joints. Testing treatments are vital to discover and protect against porosity in welding, making certain the toughness and toughness of the end product. Non-destructive screening methods such as ultrasonic testing, radiographic screening, and aesthetic assessment are generally used to identify potential issues like porosity. These methods enable the evaluation of weld top quality without jeopardizing the stability of the joint. What is Porosity.
Performing pre-weld and post-weld evaluations is likewise critical in keeping top quality control requirements. Pre-weld inspections involve verifying the materials, tools settings, and cleanliness of the job area to avoid contamination. Post-weld inspections, on the other hand, analyze the final weld for any kind of problems, including porosity, and validate that it meets defined requirements. Executing a comprehensive quality control strategy that includes detailed screening procedures and assessments is vital to decreasing porosity issues and making sure the total quality of bonded joints.
Verdict
To conclude, porosity in welding can be a common concern that influences the top quality of welds. By identifying the usual reasons of porosity and carrying out ideal practices for prevention, such as correct welding techniques and testing steps, welders can ensure excellent quality and dependable welds. It is necessary to prioritize avoidance techniques to lessen the event of porosity and preserve the integrity of welded frameworks.